arturobandini
Regular.
- Joined
- Feb 24, 2009
- Messages
- 254
- Reaction score
- 0
Today I decided to tackle the beast that is the Stainless Steel Brewery Keg.
I acquired a Keg from a friend who had bought it as a project very similar to what I've attempted today. The boiler design I had in mind was a cross between that of Aleman/Brasmwell/Damfoose's.
Tools and Equipment Cost
B&Q 740w Hammer Dril Already owned
Screwfix bi-metal holesaw set Borrowed from my Father
Small Makita Angle Grinder Already owned
Diamond Grinder Cutting Disc Already owned (Very Well Worn!!)
Kettle Elements £9.40 Tesco budget kettles
Tap FREE (Cannibalised from previous Boiler)
10gallon Keg FREE (Donated from a friend)
First I depressurised the keg by forcing down the black rubber inlet valve to release the co2. I took no chances and had the keg on it's side and aimed away from me so I didn't spear my face off. Once pressure was released I set about smashing up the Grundy connector. I had no idea how to dismantle these properly and the internet search proved fruitless too so I butchered it with grips and screwdrivers. Couldn't actually remove it in the end but it did allow me entry to the keg itself into which I poured a few litres of cold water which apparently deadens noise (wouldn't think so given the deafening sound it gave off) and stops the hot steel welding itself to the keg base. I then set about the grinding out of the lid using the grinder guard pushed against the lip of the keg as a guide (top tip from Bramswell!) and it wasn't long before the lid was cut out. I made a start yesterday and didn't wear any ear defenders and my ears were ringing all night. Wet some cotton wool and shoved it in my ears today and it worked a treat.
The hole was fairly straightforward and I angled the grinder afterwards so as to cut away any lose burrs but it will need filing. I then cut the lip of the keg either side of the handles (Aleman's idea for Damfoose's Keg I think) to remove excess weight and make it easier to tip the trub and hops at the end. I chose a spot fairly close to the handle grip and cut down to the top of the keg fairly quickly. A glance at the Diamond blade told me I was closer to Zircons than Diamonds now as there was hardly any cutting blade left. I forged on regardless and brought the mighty Japanese Grinder down on the other side of the handle only for it to stick halfway down the cut. Bugger! I quickly pulled the plug and couldn't budge the grinder from the cut. Quick hammering later and the cutting disc was bent out of shape so no more grinding till I get my hands on another.
Now the fabled hole cutting in stainless steel time! I decided to do the two 40mm kettle element holes first and got the cheapo screwfix cutter ready in the even cheaper drill. I thought that if I was going to knacker any power tool I'd use the glorified screwdriver. The first hole was remarkably straight forward and with a few breaks for water cooling it cut nice and neatly. The second hole took a bit more patience but it cut well in the end and I had my two kettle element holes done with a minimum of fuss. Looking at the Screwfix cutter though it had cut it's last hole; scorched, deformed and almost blunt it had served me well.
I put a 25mm cutter into the drill and set about the tap hole. This one proved an absolute mother and took 3 times as long as the other two combined. The pilot hole just wouldn't bite through the steel and I work hardened the area with prolonged attempts. In the end I ground down the pilot drill bit to a stump and had to switch arbors to the bigger size to finish the pilot. When that was done both drill bits had melted under the heat and pressure of the hole cutting. I loosened the drill bits and made them longer so as to keep the bit in the hole for 25mm cutter. The actual cutting of the hole was fairly quick and the screwfix bi-metal cutters didn't fail me.
So now I have one knackered grinding disc, two banjaxed drill bits, a keg with the lid off, the handles part cut, two 40mm holes and a 25mm hole needing filing.
The back of the beast has been broken but there is still a little more work to do to pretty the thing up and finish the handles. Hopefully yoink a cutting disc off my Dad tomorrow but I definitely won't be telling him what happened to his holesaw kit.
As the Kettle looks now
Tap hole the dirty mother
Inside the Kettle view of element cut outs
Outside view of the element cut outs...burn baby burn
Alas poor cutting disc
Edit - Pictures Added
I acquired a Keg from a friend who had bought it as a project very similar to what I've attempted today. The boiler design I had in mind was a cross between that of Aleman/Brasmwell/Damfoose's.
Tools and Equipment Cost
B&Q 740w Hammer Dril Already owned
Screwfix bi-metal holesaw set Borrowed from my Father
Small Makita Angle Grinder Already owned
Diamond Grinder Cutting Disc Already owned (Very Well Worn!!)
Kettle Elements £9.40 Tesco budget kettles
Tap FREE (Cannibalised from previous Boiler)
10gallon Keg FREE (Donated from a friend)
First I depressurised the keg by forcing down the black rubber inlet valve to release the co2. I took no chances and had the keg on it's side and aimed away from me so I didn't spear my face off. Once pressure was released I set about smashing up the Grundy connector. I had no idea how to dismantle these properly and the internet search proved fruitless too so I butchered it with grips and screwdrivers. Couldn't actually remove it in the end but it did allow me entry to the keg itself into which I poured a few litres of cold water which apparently deadens noise (wouldn't think so given the deafening sound it gave off) and stops the hot steel welding itself to the keg base. I then set about the grinding out of the lid using the grinder guard pushed against the lip of the keg as a guide (top tip from Bramswell!) and it wasn't long before the lid was cut out. I made a start yesterday and didn't wear any ear defenders and my ears were ringing all night. Wet some cotton wool and shoved it in my ears today and it worked a treat.
The hole was fairly straightforward and I angled the grinder afterwards so as to cut away any lose burrs but it will need filing. I then cut the lip of the keg either side of the handles (Aleman's idea for Damfoose's Keg I think) to remove excess weight and make it easier to tip the trub and hops at the end. I chose a spot fairly close to the handle grip and cut down to the top of the keg fairly quickly. A glance at the Diamond blade told me I was closer to Zircons than Diamonds now as there was hardly any cutting blade left. I forged on regardless and brought the mighty Japanese Grinder down on the other side of the handle only for it to stick halfway down the cut. Bugger! I quickly pulled the plug and couldn't budge the grinder from the cut. Quick hammering later and the cutting disc was bent out of shape so no more grinding till I get my hands on another.
Now the fabled hole cutting in stainless steel time! I decided to do the two 40mm kettle element holes first and got the cheapo screwfix cutter ready in the even cheaper drill. I thought that if I was going to knacker any power tool I'd use the glorified screwdriver. The first hole was remarkably straight forward and with a few breaks for water cooling it cut nice and neatly. The second hole took a bit more patience but it cut well in the end and I had my two kettle element holes done with a minimum of fuss. Looking at the Screwfix cutter though it had cut it's last hole; scorched, deformed and almost blunt it had served me well.
I put a 25mm cutter into the drill and set about the tap hole. This one proved an absolute mother and took 3 times as long as the other two combined. The pilot hole just wouldn't bite through the steel and I work hardened the area with prolonged attempts. In the end I ground down the pilot drill bit to a stump and had to switch arbors to the bigger size to finish the pilot. When that was done both drill bits had melted under the heat and pressure of the hole cutting. I loosened the drill bits and made them longer so as to keep the bit in the hole for 25mm cutter. The actual cutting of the hole was fairly quick and the screwfix bi-metal cutters didn't fail me.
So now I have one knackered grinding disc, two banjaxed drill bits, a keg with the lid off, the handles part cut, two 40mm holes and a 25mm hole needing filing.
The back of the beast has been broken but there is still a little more work to do to pretty the thing up and finish the handles. Hopefully yoink a cutting disc off my Dad tomorrow but I definitely won't be telling him what happened to his holesaw kit.
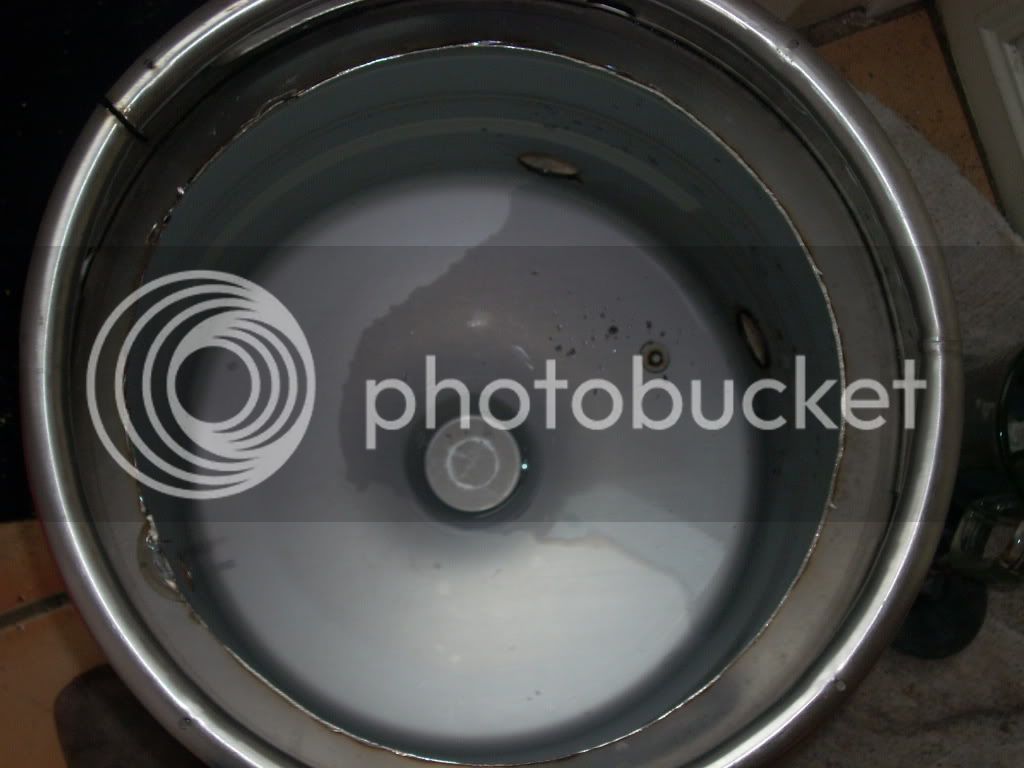
As the Kettle looks now
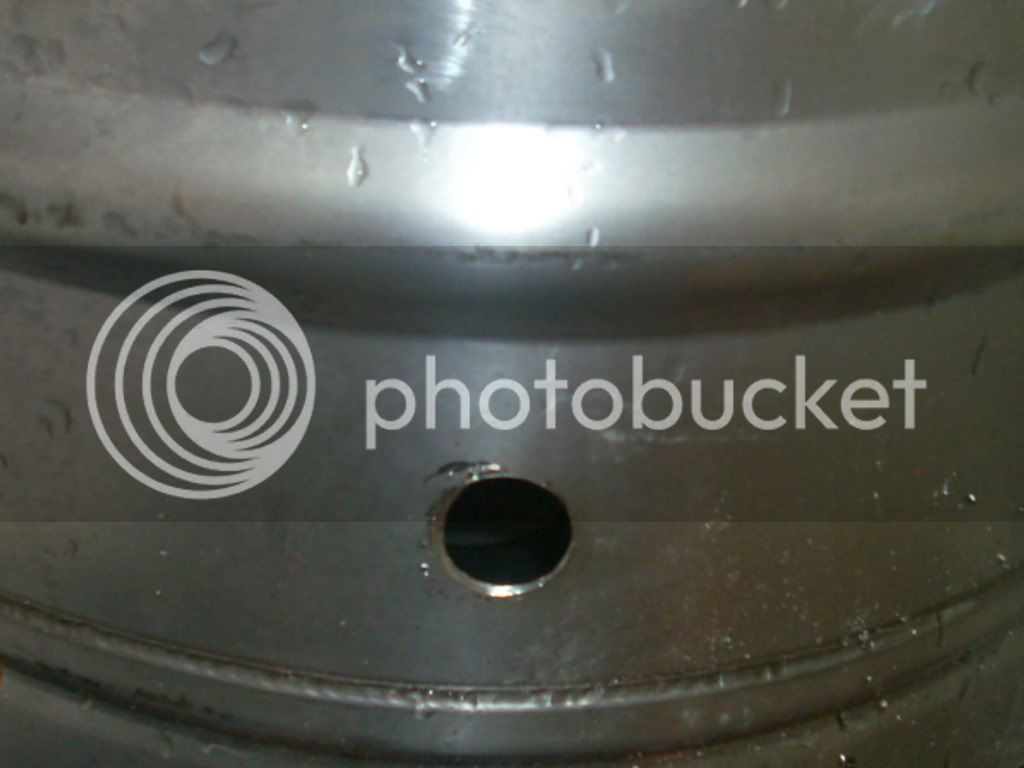
Tap hole the dirty mother
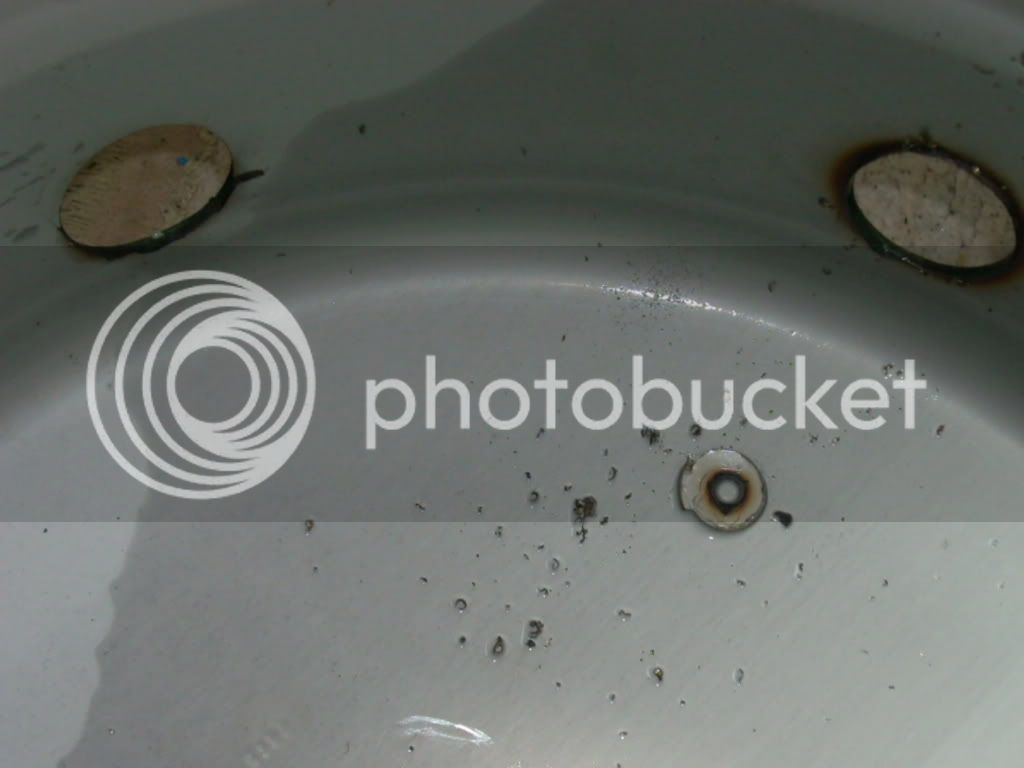
Inside the Kettle view of element cut outs
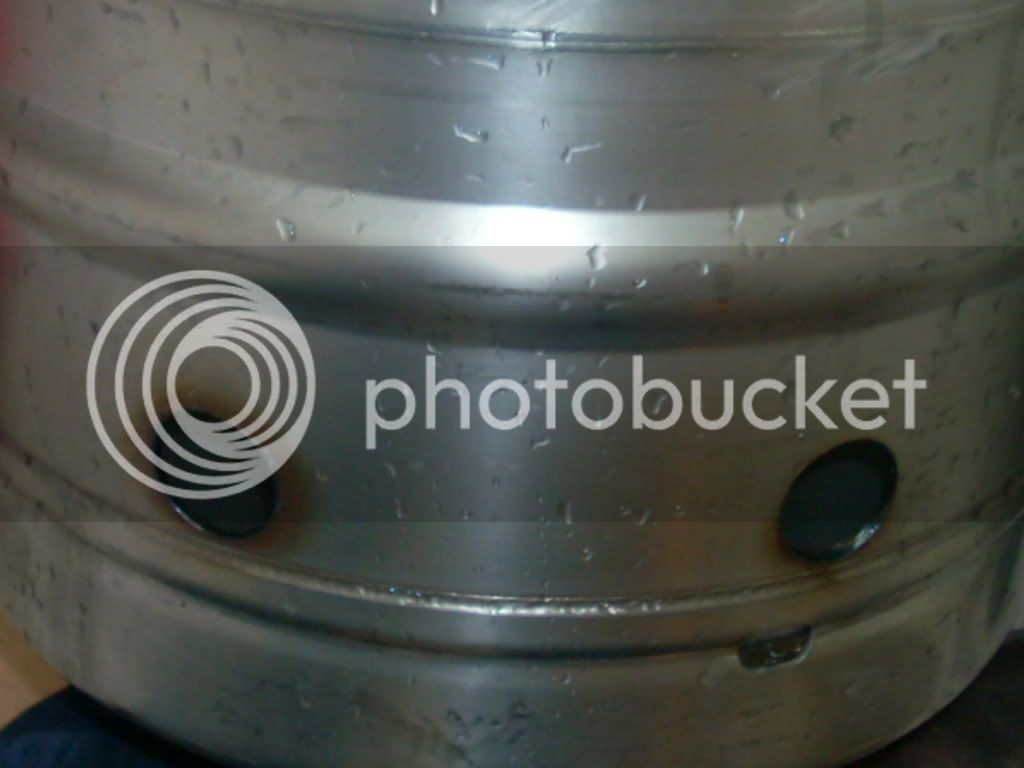
Outside view of the element cut outs...burn baby burn
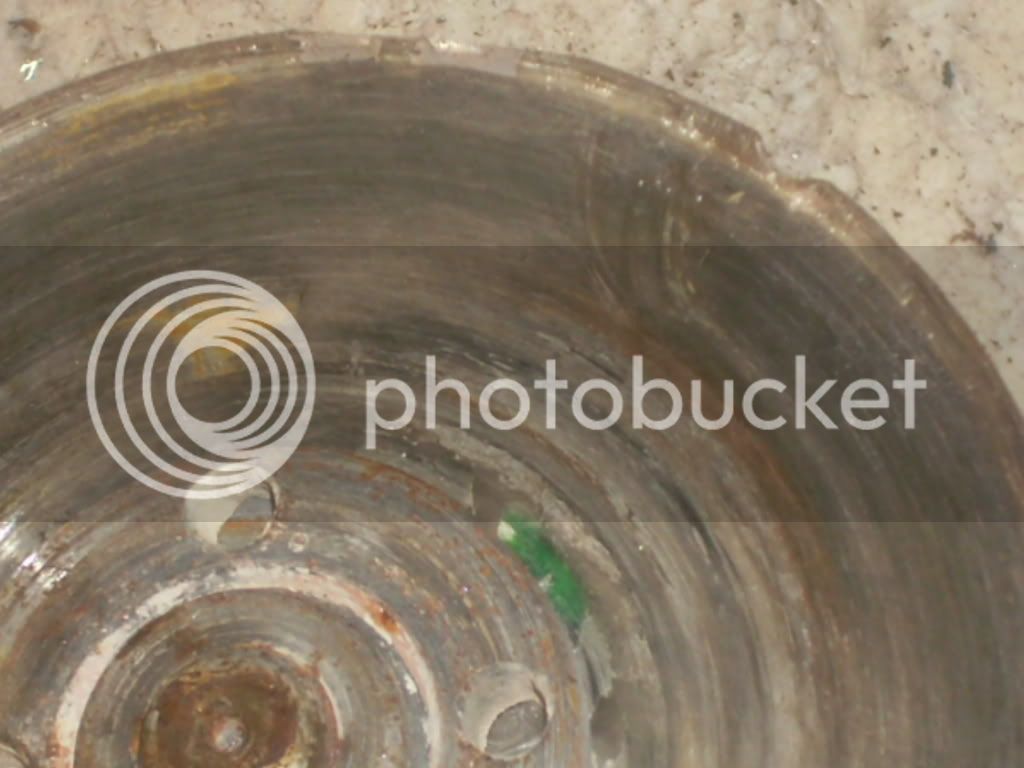
Alas poor cutting disc
Edit - Pictures Added