I thought it may be of interest to show the construction of an adapter to allow the use of alternate sources of CO2 with plastic barrels having the usual S30 connector.
I only have the gas cylinder-type connectors rather than the bulb ones, but I think this adapter will work with both. In essence it converts the M18x2 thread the S30 uses to a standard ½ inch BSP, so you can connect pretty much anything onto that. I added a John Guest connector and charge my barrels via a ¼ inch pressure line. Unlike some converters, you don't need to remove the non-return valve, this adapter will take enough pressure to open the non-return valve and gas up the barrel. Hence you don't need to leave the gas on all the time.
A slight problem is that it isn't cheap but as, really, you only need the one, to occasionally recharge barrels, I don't think this is too much of a problem.
You need to get a converter that allows the use of CO2 bulbs on gas cylinder-type connectors (basically this adds the spiky thing in the middle to an S30 connector). An example of this is "8 grm BULB ADAPTOR - BRASS" from Hop & Grape (their code GAG20212745). You also need a compression type blanking fitting for 15mm copper pipe (available at DIY store), solder and a blowtorch. Ensure the plumbing fitting has a flat blanking face.
First, hacksaw the converter into two parts, just above the flats, as true as you can. If youâre like me, the saw will go adrift (as you can see!). Discard the top half (the bit with the male thread). File down the newly sawn face on the other bit to get it flat, perpendicular to the axis of the body of the valve and smooth. Now, an important bit: remove the rubber seal from the converterâs female threaded end.
Use the blowtorch to heat up the half of the converter and tin the top surface with solder. I did this with the converter on a piece of wood, to insulate it and protect what was under it from heat damage. I also banged a large headed nail through the piece of wood to put the body of the converter over that, so as to keep it still while soldering. Donât overdo the solder, it doesnât need huge lumps of it, just enough to completely cover the brass with a thin layer of solder.
Similarly, tin the flat face of the body of the blanking connector. It will probably help if you give this a quick rub over with wet and dry paper, to clean it a bit, to allow the solder to âtakeâ.
Now, put the two bits together, tinned face to tinned face, and heat them. I put the converter bit on the nail again, and the plumbing fitting on top of it. As you see the solder melt, and the two bits settle together, quickly go around the circumference of the joint with the solder, melting a bit more solder into the joint. It will get sucked in through capillary action. Again, donât go mad with the solder, just a bit more. While itâs still molten, check and adjust the alignment of the two bits, gently pushing them about as required. Keep the work hot while youâre doing this, but donât spend too long at it or the work will overheat and weaken the joint. It doesnât have to be precisely centred. Leave the work to cool naturally, and donât move it again till itâs cooled.
Finally, extend the hole thatâs in the converter half of your new adapter through the blanking face of the plumbing fitting and replace the rubber seal in the converter thread. Job done.
I found I needed an extra gasket in the ½-inch BSP female fitting to get a gas-tight seal, as there wasnât quite enough thread to fully tighten the fitting on due to the hex flats on the plumbing fitting.
Yes, before anyone tells me, I do know that solder is not really suitable for high-pressure gas fittings. If you have access to the technology, you could braze or silver-solder maybe, instead. However, I would point out that 1/ the faces of the joint are quite large compared to the area that is taking the gas pressure 2/ the pressure will only be intermittent 3/ the pressure shouldnât be that high â only a few tens of PSI, I believe. But, itâs your workmanship and you do this at your own risk. If youâre not confident about being able to make a good soldered joint Iâd advise you donât try this.
I only have the gas cylinder-type connectors rather than the bulb ones, but I think this adapter will work with both. In essence it converts the M18x2 thread the S30 uses to a standard ½ inch BSP, so you can connect pretty much anything onto that. I added a John Guest connector and charge my barrels via a ¼ inch pressure line. Unlike some converters, you don't need to remove the non-return valve, this adapter will take enough pressure to open the non-return valve and gas up the barrel. Hence you don't need to leave the gas on all the time.
A slight problem is that it isn't cheap but as, really, you only need the one, to occasionally recharge barrels, I don't think this is too much of a problem.
You need to get a converter that allows the use of CO2 bulbs on gas cylinder-type connectors (basically this adds the spiky thing in the middle to an S30 connector). An example of this is "8 grm BULB ADAPTOR - BRASS" from Hop & Grape (their code GAG20212745). You also need a compression type blanking fitting for 15mm copper pipe (available at DIY store), solder and a blowtorch. Ensure the plumbing fitting has a flat blanking face.
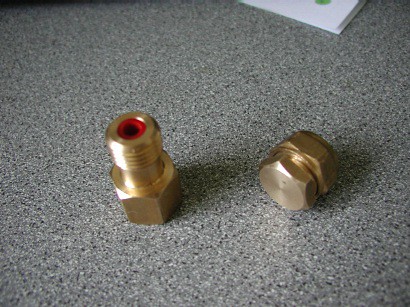
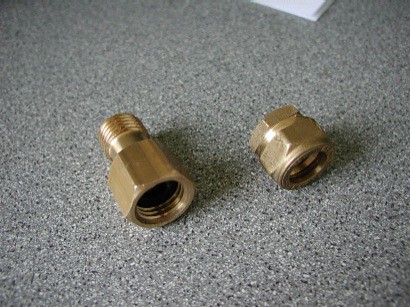
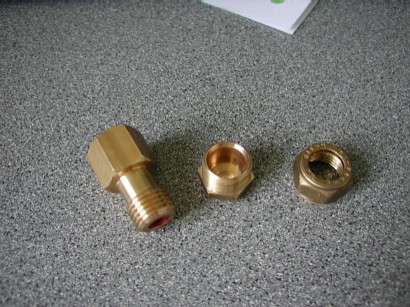
First, hacksaw the converter into two parts, just above the flats, as true as you can. If youâre like me, the saw will go adrift (as you can see!). Discard the top half (the bit with the male thread). File down the newly sawn face on the other bit to get it flat, perpendicular to the axis of the body of the valve and smooth. Now, an important bit: remove the rubber seal from the converterâs female threaded end.
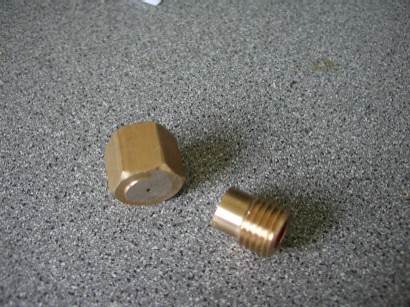
Use the blowtorch to heat up the half of the converter and tin the top surface with solder. I did this with the converter on a piece of wood, to insulate it and protect what was under it from heat damage. I also banged a large headed nail through the piece of wood to put the body of the converter over that, so as to keep it still while soldering. Donât overdo the solder, it doesnât need huge lumps of it, just enough to completely cover the brass with a thin layer of solder.
Similarly, tin the flat face of the body of the blanking connector. It will probably help if you give this a quick rub over with wet and dry paper, to clean it a bit, to allow the solder to âtakeâ.
Now, put the two bits together, tinned face to tinned face, and heat them. I put the converter bit on the nail again, and the plumbing fitting on top of it. As you see the solder melt, and the two bits settle together, quickly go around the circumference of the joint with the solder, melting a bit more solder into the joint. It will get sucked in through capillary action. Again, donât go mad with the solder, just a bit more. While itâs still molten, check and adjust the alignment of the two bits, gently pushing them about as required. Keep the work hot while youâre doing this, but donât spend too long at it or the work will overheat and weaken the joint. It doesnât have to be precisely centred. Leave the work to cool naturally, and donât move it again till itâs cooled.
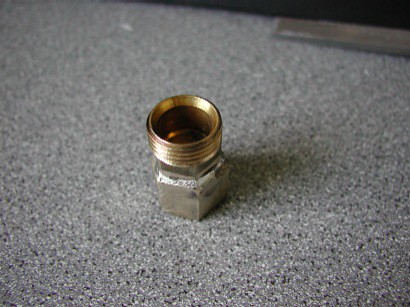
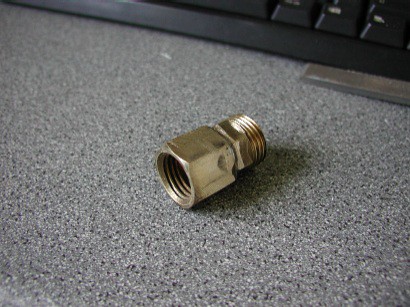
Finally, extend the hole thatâs in the converter half of your new adapter through the blanking face of the plumbing fitting and replace the rubber seal in the converter thread. Job done.
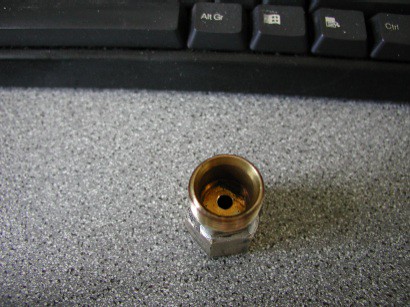
I found I needed an extra gasket in the ½-inch BSP female fitting to get a gas-tight seal, as there wasnât quite enough thread to fully tighten the fitting on due to the hex flats on the plumbing fitting.
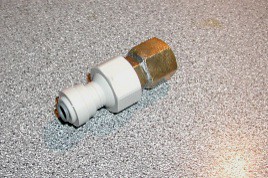
Yes, before anyone tells me, I do know that solder is not really suitable for high-pressure gas fittings. If you have access to the technology, you could braze or silver-solder maybe, instead. However, I would point out that 1/ the faces of the joint are quite large compared to the area that is taking the gas pressure 2/ the pressure will only be intermittent 3/ the pressure shouldnât be that high â only a few tens of PSI, I believe. But, itâs your workmanship and you do this at your own risk. If youâre not confident about being able to make a good soldered joint Iâd advise you donât try this.