Northern Brewer
Landlord.
I haven't got a name for the brewery yet so I've taken Frisp's suggestion as a temporary name. I've now started construction proper, I've been tinkering with things however it was mainly to test how things work and to make sure I've got all the bits I need,
I thought I would start with the heat exchangers for HERMS. I originally bought an asparagus steamer however changed my mind and bought a 6L Thermos pot and may use the steamer for a hopback later, or just veg.
Here's most of the components.
There's a few bits like 16mm silicon o-rings and PTFE tape missing and I have some bits to buy, some heat resistant flex and a cable gland but apart from that its complete. The plumbing bits are :-
9m of 10mm copper tube bent around a 160mm drainage pipe
4 x 10mm capillary elbows
2 x 10mm to 3/8" BSP brass compression adaptors
2 x 3/8" to 1/2" BSP socket adaptors - stainless
2 x 1/2" hosetails - may change these but useful for pressure testing
1 x 3KW immersion heater from Backer
tools - except usual stuff
1 1/8" hole saw
51mm hole saw
16mm qmax cutter - all these I already had
Coil after soldering capillary fittings, trying it for size and marking it up for the holes.
Marking up the hole ready for drilling with the 1 1/8" hole saw, want to get the hole right up against the top edge wiithout damaging it
This is the hole ready for the smaller hole in the inner skin
Making sure the 3/8" to 1/2" adaptor fits
Making the inner 16mm hole with the Qmax
Coil and fitting inserted, took a bit of wiggling to get it in, I put a thin 16mm silicon o-ring both sides of the inner skin and puts lots of PTFE on the 3/8" thread that goes through the inner skin, a bit fiddley being recessed.
Underneath the pot, outer skin drilled to 51mm, could be smaller, the elements prongs are about 30mm apart.
the inner skin drilled with a 1/2" drill and the element inserted. The lead is off of a Tesco kettle and is just for testing, the final version will have a chunkier lead with ring solder terminals on the end to go on the element and I'll drill a hole to bolt the earth too. Will also add a cover. The lead comes through the side of the pot at the bootom though the insulation and will terminate directly on a Commando plug.
Mostly finished, the pipework has been pressure tested but I haven't filled the pot and tested the element yet.
False bottom for mash tun
I roughed it out about 3mm oversize using a nibbler then stuck on a more accurate thin card template with Pritt glue then tidied it up with the angle grinder. I then put stainless kitchen door handles on both side, these lift the FB off the bottom of the pot and provide handles for lifting it out. I'll be putting the hose around it for the seal once i have built a little jig with a stanley blade in to cut the beer line longtitudinally, first attempt wasn't up to much.
Cheers
NB
I thought I would start with the heat exchangers for HERMS. I originally bought an asparagus steamer however changed my mind and bought a 6L Thermos pot and may use the steamer for a hopback later, or just veg.
Here's most of the components.
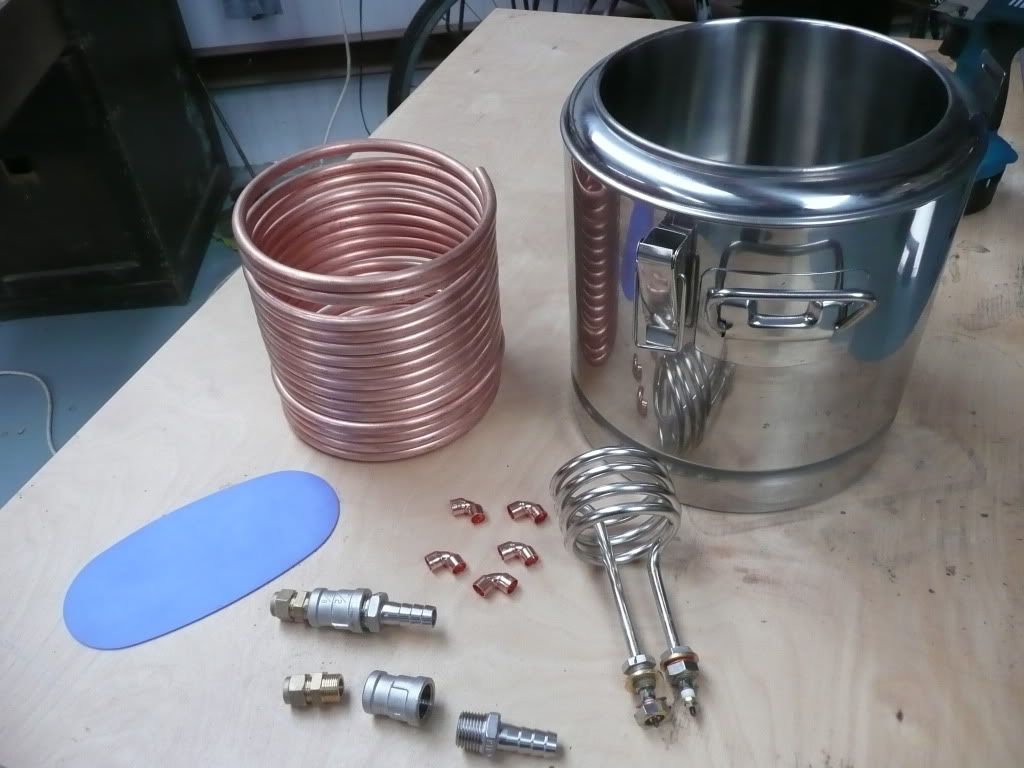
There's a few bits like 16mm silicon o-rings and PTFE tape missing and I have some bits to buy, some heat resistant flex and a cable gland but apart from that its complete. The plumbing bits are :-
9m of 10mm copper tube bent around a 160mm drainage pipe
4 x 10mm capillary elbows
2 x 10mm to 3/8" BSP brass compression adaptors
2 x 3/8" to 1/2" BSP socket adaptors - stainless
2 x 1/2" hosetails - may change these but useful for pressure testing
1 x 3KW immersion heater from Backer
tools - except usual stuff
1 1/8" hole saw
51mm hole saw
16mm qmax cutter - all these I already had
Coil after soldering capillary fittings, trying it for size and marking it up for the holes.
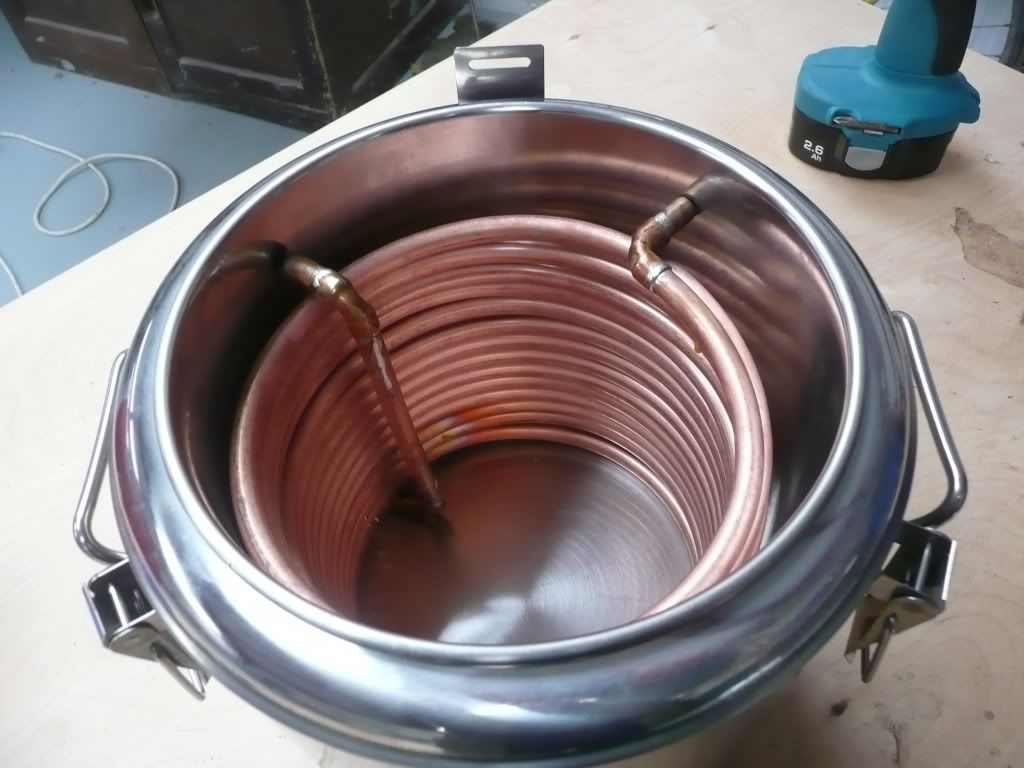
Marking up the hole ready for drilling with the 1 1/8" hole saw, want to get the hole right up against the top edge wiithout damaging it
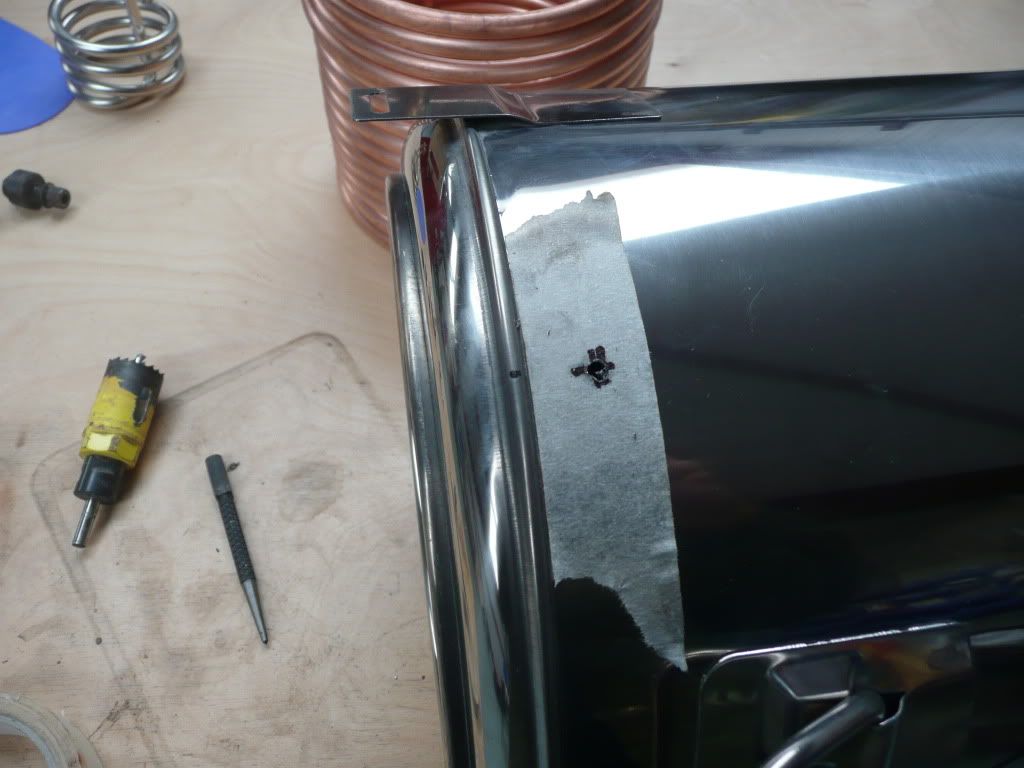
This is the hole ready for the smaller hole in the inner skin
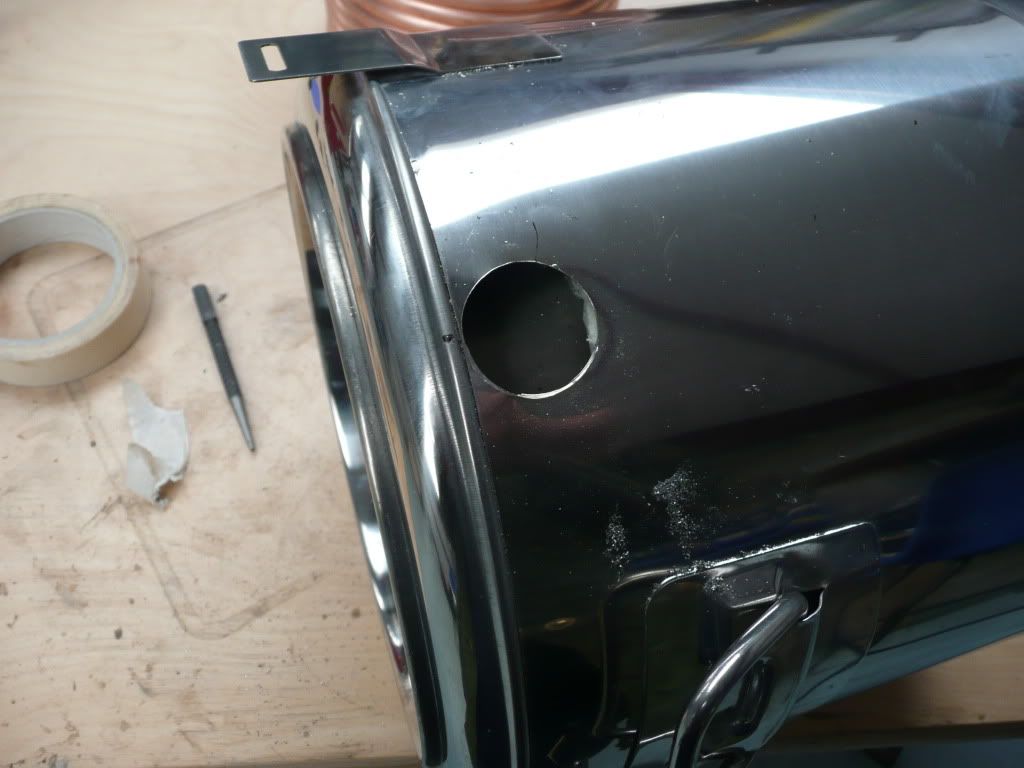
Making sure the 3/8" to 1/2" adaptor fits
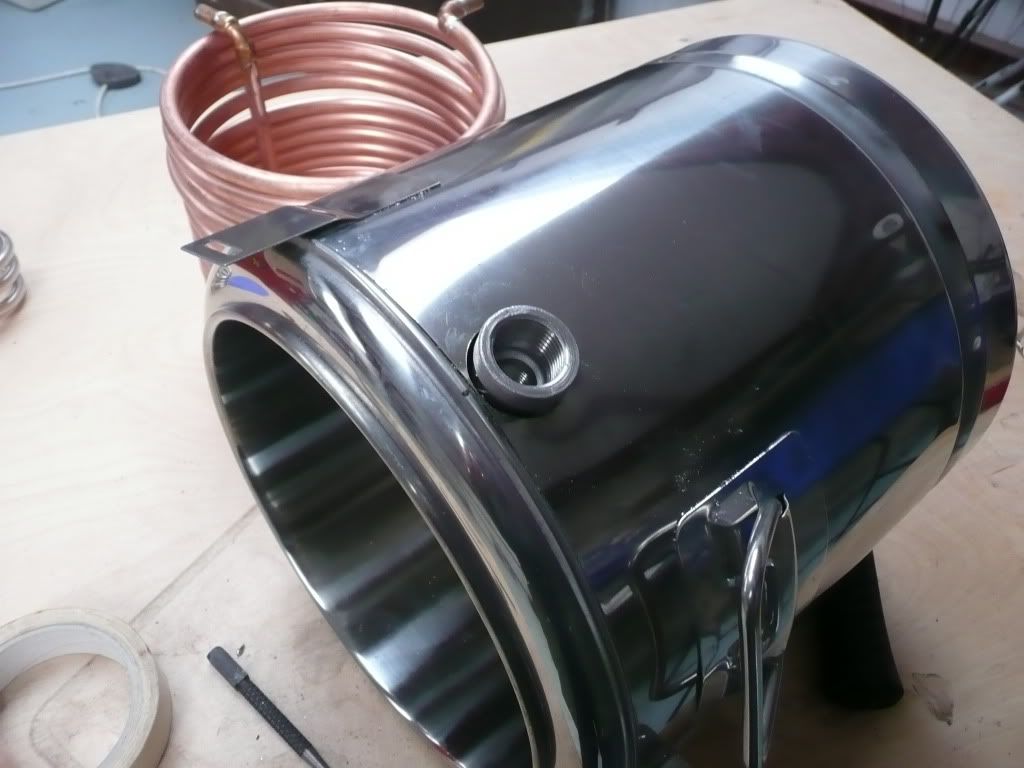
Making the inner 16mm hole with the Qmax
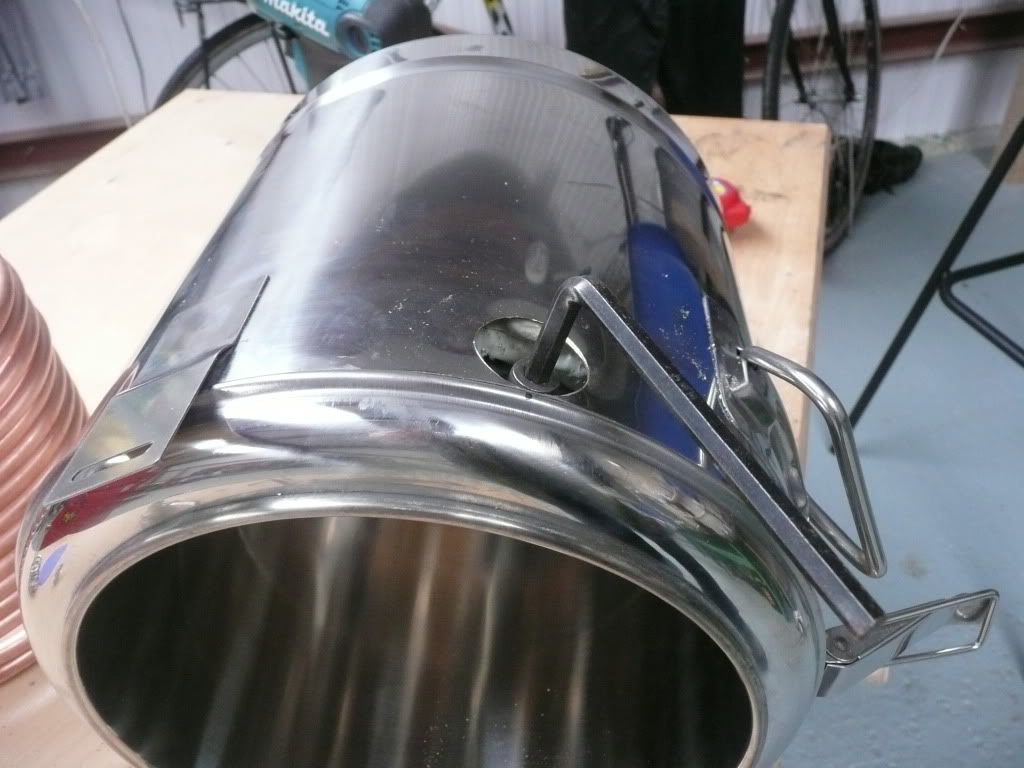
Coil and fitting inserted, took a bit of wiggling to get it in, I put a thin 16mm silicon o-ring both sides of the inner skin and puts lots of PTFE on the 3/8" thread that goes through the inner skin, a bit fiddley being recessed.
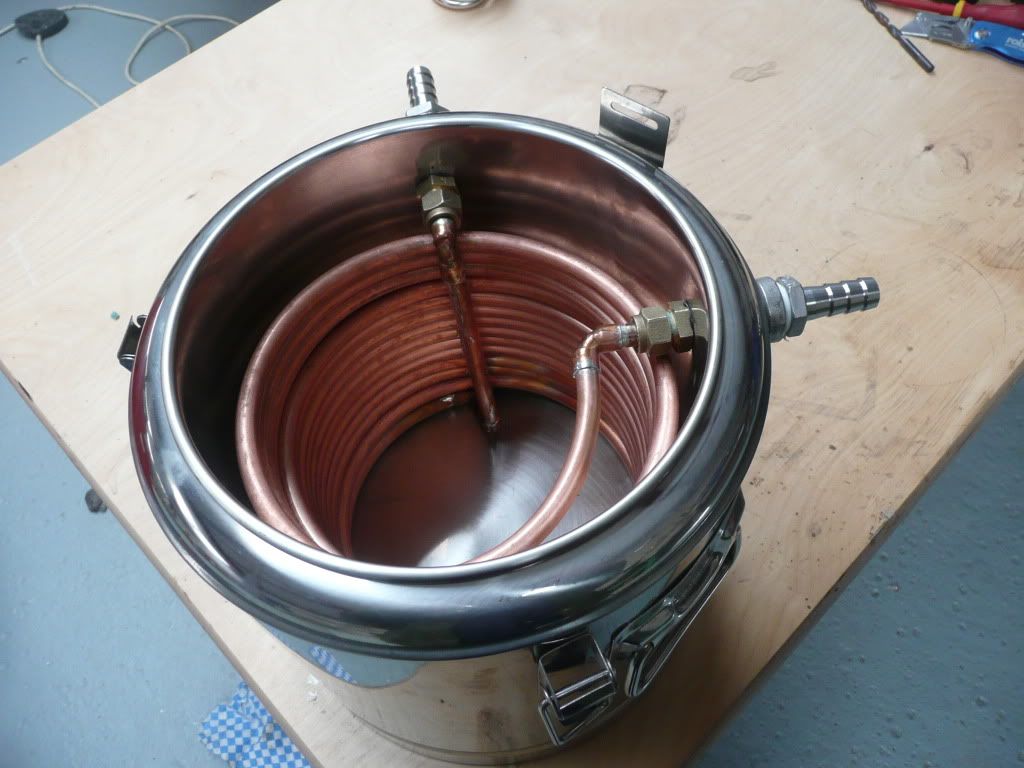
Underneath the pot, outer skin drilled to 51mm, could be smaller, the elements prongs are about 30mm apart.
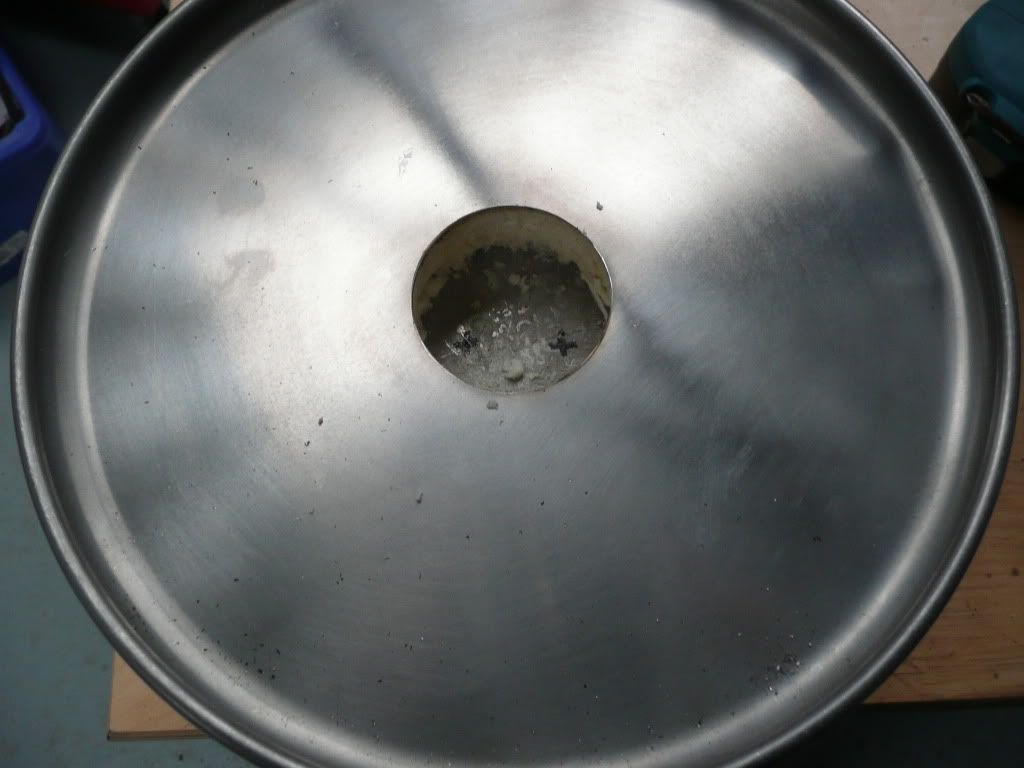
the inner skin drilled with a 1/2" drill and the element inserted. The lead is off of a Tesco kettle and is just for testing, the final version will have a chunkier lead with ring solder terminals on the end to go on the element and I'll drill a hole to bolt the earth too. Will also add a cover. The lead comes through the side of the pot at the bootom though the insulation and will terminate directly on a Commando plug.
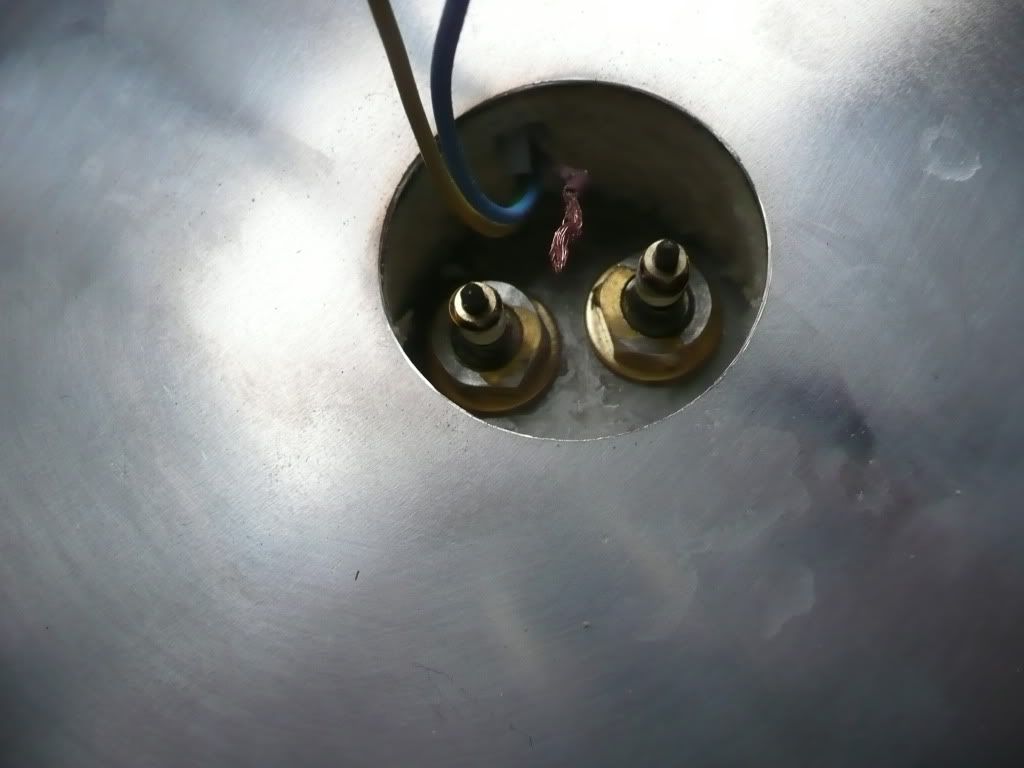
Mostly finished, the pipework has been pressure tested but I haven't filled the pot and tested the element yet.
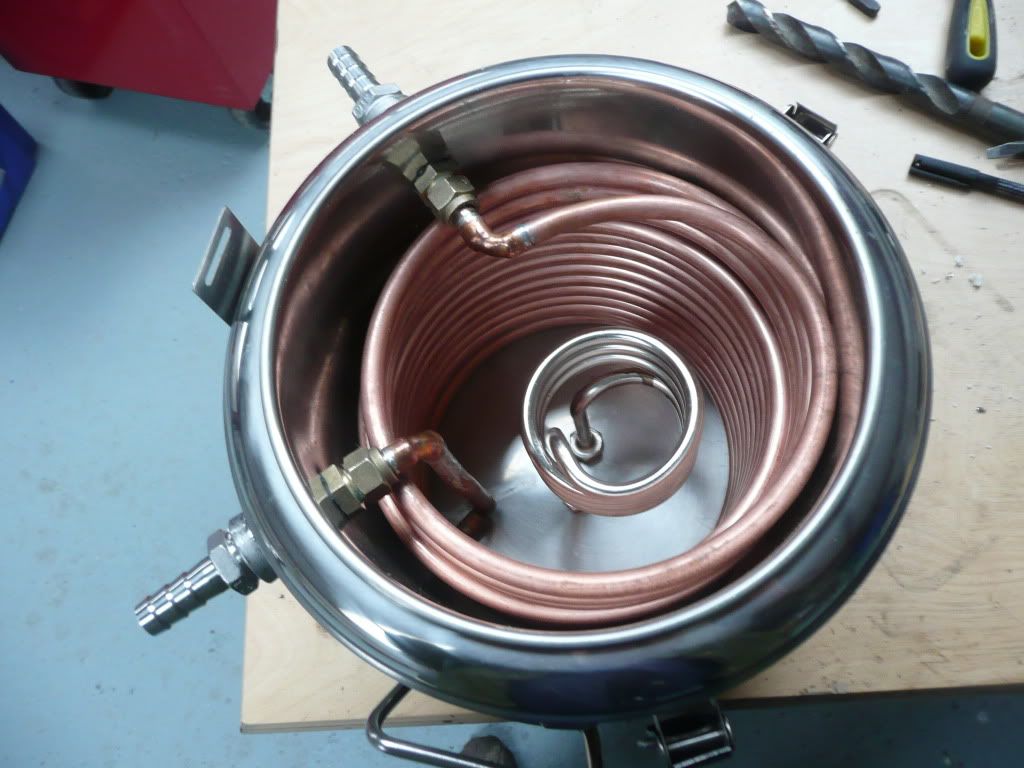
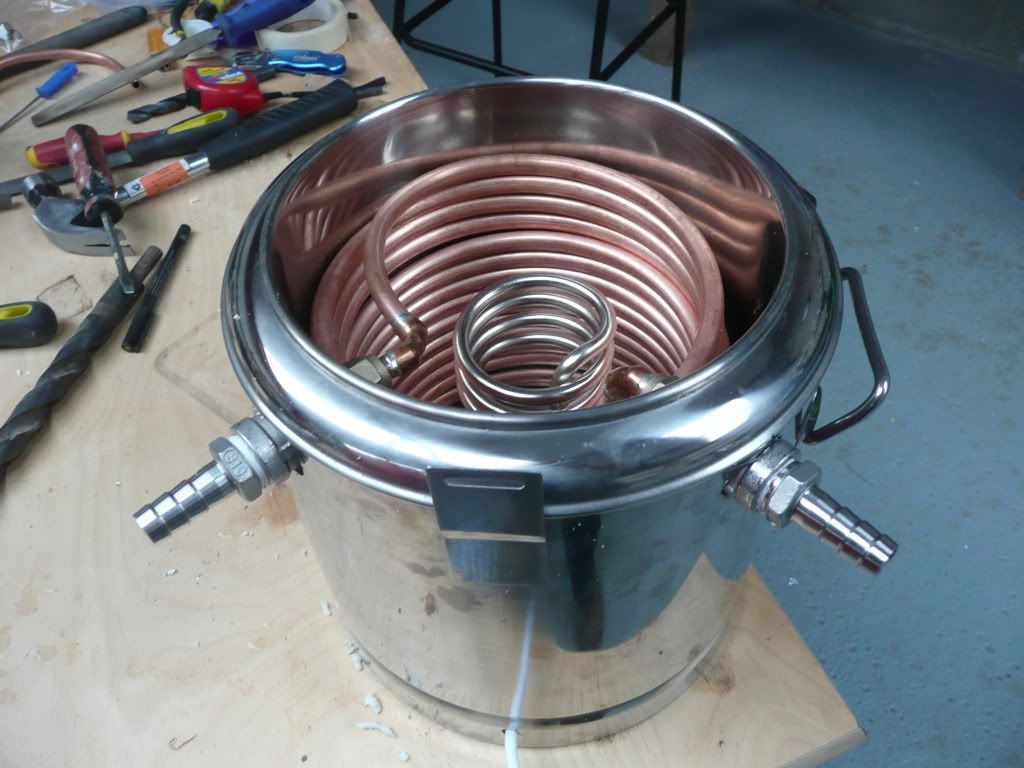
False bottom for mash tun
I roughed it out about 3mm oversize using a nibbler then stuck on a more accurate thin card template with Pritt glue then tidied it up with the angle grinder. I then put stainless kitchen door handles on both side, these lift the FB off the bottom of the pot and provide handles for lifting it out. I'll be putting the hose around it for the seal once i have built a little jig with a stanley blade in to cut the beer line longtitudinally, first attempt wasn't up to much.
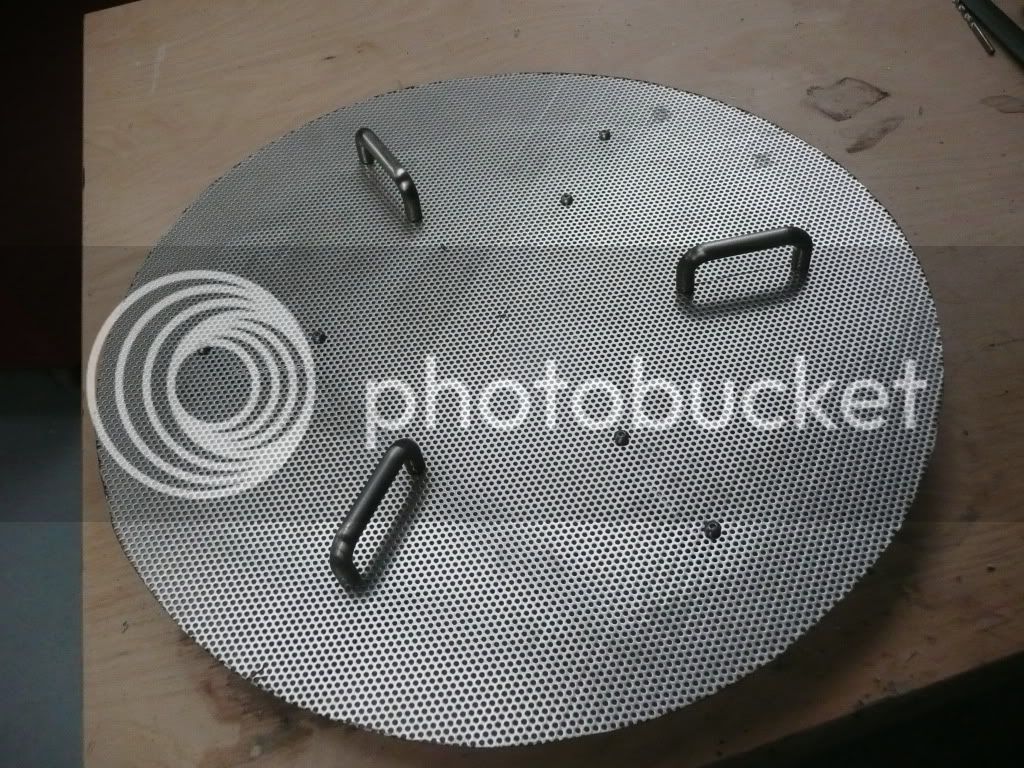
Cheers
NB